Als Produktionsstandort besitzt Deutschland die herausragende Stärke, technisch anspruchsvolle und qualitativ hochwertige Produkte herzustellen. Seitens der Unternehmen erfordert dies ein hohes Maß an Dynamik, Wandlungsfähigkeit und Kundenorientierung (vgl. Gausemeier/Wiendahl). Bereits seit den 1980er Jahren wird die Produkt-Entwicklung durch digitale Hilfsmittel unterstützt. Zuerst begrenzt auf die Übernahme einzelner Funktionalitäten, ergänzen digitale Hilfsmittel und Werkzeuge heute über den gesamten Prozess der Produktentwicklung hinweg. Darüber hinaus ermöglichen sie eine rechtssichere Dokumentation und die standort- und firmenübergreifende Zusammenarbeit.
Viele der heute eingesetzten Software-Lösungen haben ihren Ursprung in der Zeit der CIM-Euphorie und wurden mit dem Ziel der Realisierung einer durchgängig digitalen Fabrik entwickelt. CAD- und PLM-Systeme sowie unzählige Spezialsoftware für meist anwendungs- oder fachspezifische Fragestellungen prägen inzwischen den Entwicklerarbeitsplatz.
Über den Arbeitsplatz hinaus werden heute vermehrt Arbeitsprozesse digitalisiert. Beispiele dafür sind Simulationen sowie hybride Test- und Versuchsläufe, digitale Prototypen und der vermehrte Einsatz von Systemen. Abhängig von Unternehmensgröße und Branche schwankt der Durchdringungsgrad der einzelnen Lösungen.
Neu hinzugekommen ist in den letzten Jahren vermehrt der Einsatz von Hilfsmitteln zur besseren Zusammenarbeit von Projektbeteiligten und zur Unterstützung des Projektmanagements durch Collaboration-Tools. Eng damit verbunden werden vermehrt Anstrengungen unternommen, den hohen Grad der Digitalisierung der Produktentwicklung auf die nachfolgenden Unternehmensprozesse zu übertragen bzw. diese miteinander zu verknüpfen.
Angetrieben wird diese Entwicklung von der Anforderung immer kürzerer Entwicklungszyklen sowie der Erfahrung, dass Informationsaustausch zu den nachfolgenden produktionsnahen Prozessschritten vielfach nur unzureichend realisiert wird. Die Durchgängigkeit des Engineerings im Sinne eines vereinfachten, schnellen und zuverlässigen Datenaustauschs entlang des Produktlebenszyklus wird aus diesem Grund als eines der wesentlichen Potentiale von Industrie 4.0 angesehen. Der dafür notwendige Aufwand, Schwierigkeiten der Datenintegration in den einzelnen IT-Systemen, sowie Vorbehalte hinsichtlich der Datensicherheit bzw. des Know-how-Schutzes einzelner Partner stellen gegenwärtig die zentralen Barrieren dar. Sinkende Kosten für Sensordatenerfassung, Speicherplatz und Rechenkapazität stellen andererseits jedoch große Chancen für neue Lösungen in Aussicht.
Sie wollen zukünftig wettbewerbsfähig bleiben oder haben weitere Fragen rund um das Thema PDM und PLM? Kontaktieren Sie uns unter 0231/562214-40 oder über unser Kontaktformular.
Quelle: Digitalisierung industrieller Arbeit – Die Vision Industrie 4.0 und ihre sozialen Herausforderungen, H. Hirsch-Kreinsen, P. Ittermann, 2015
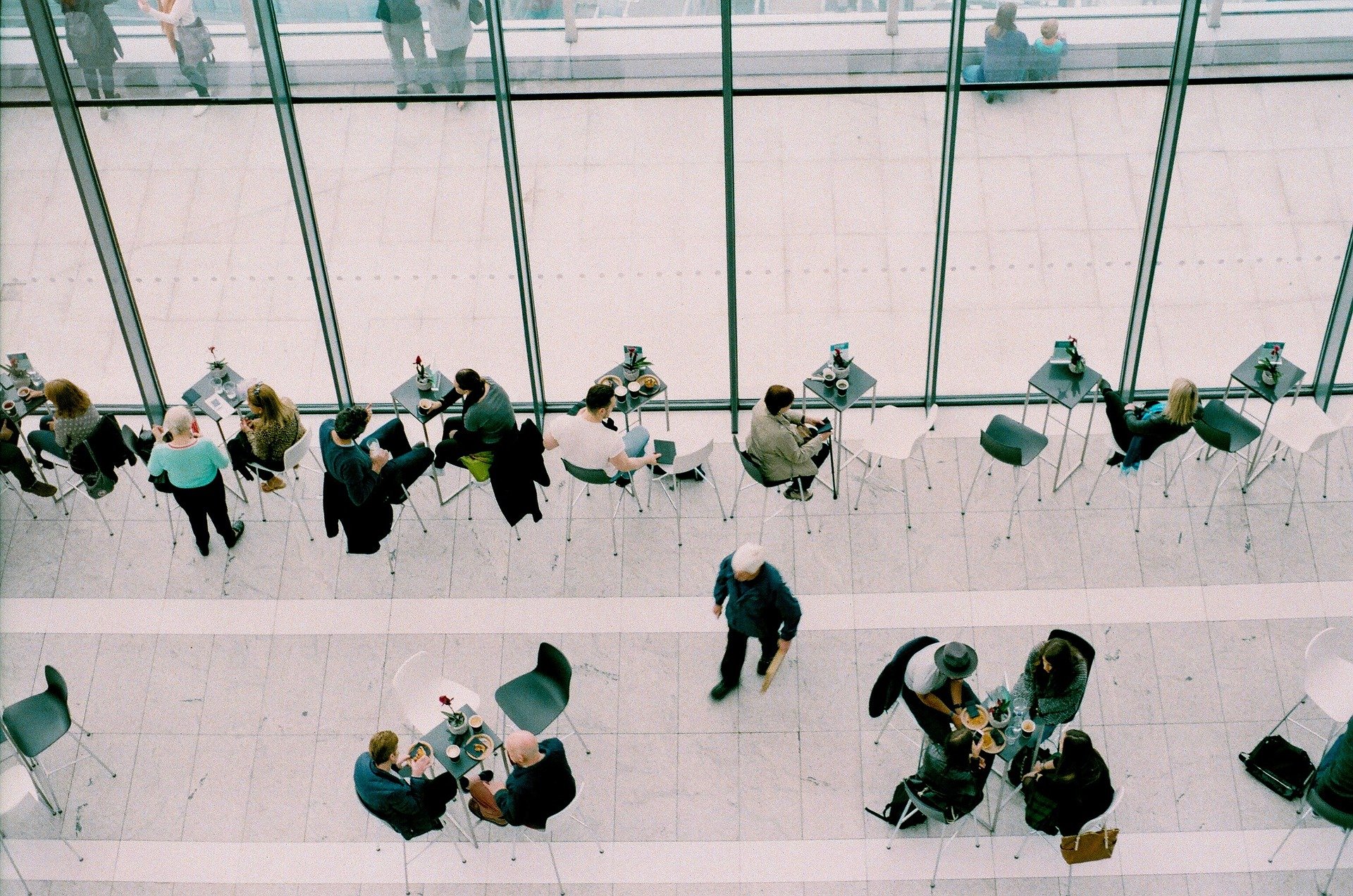